Technical Glossary
Gear Types
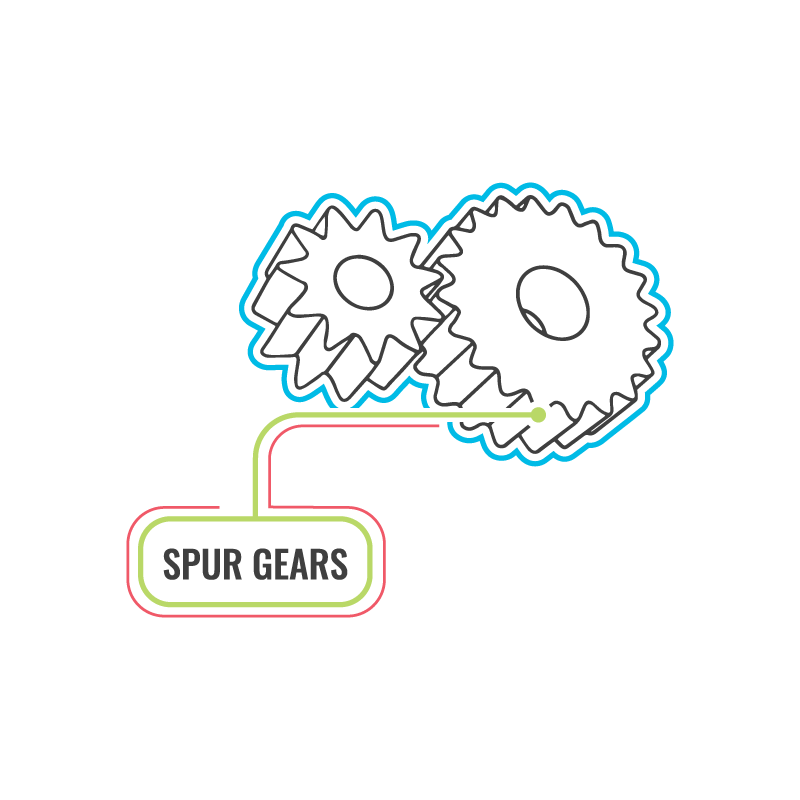
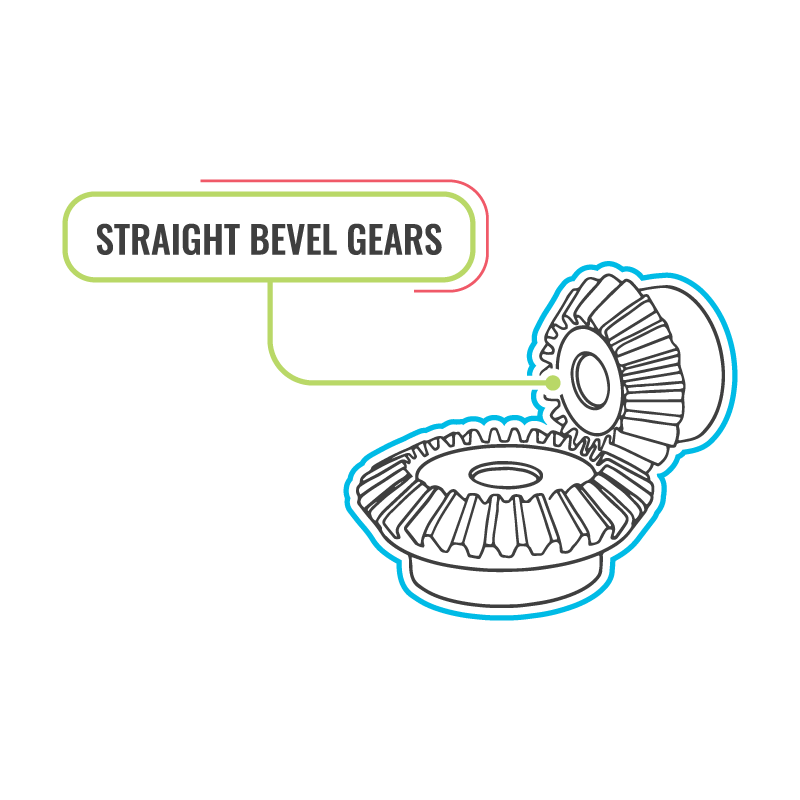
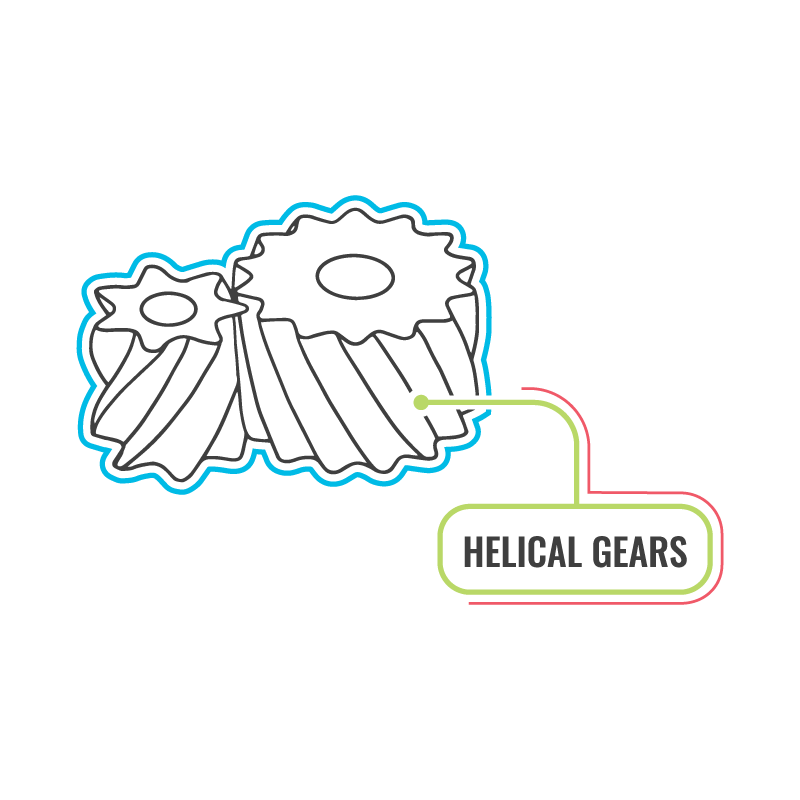
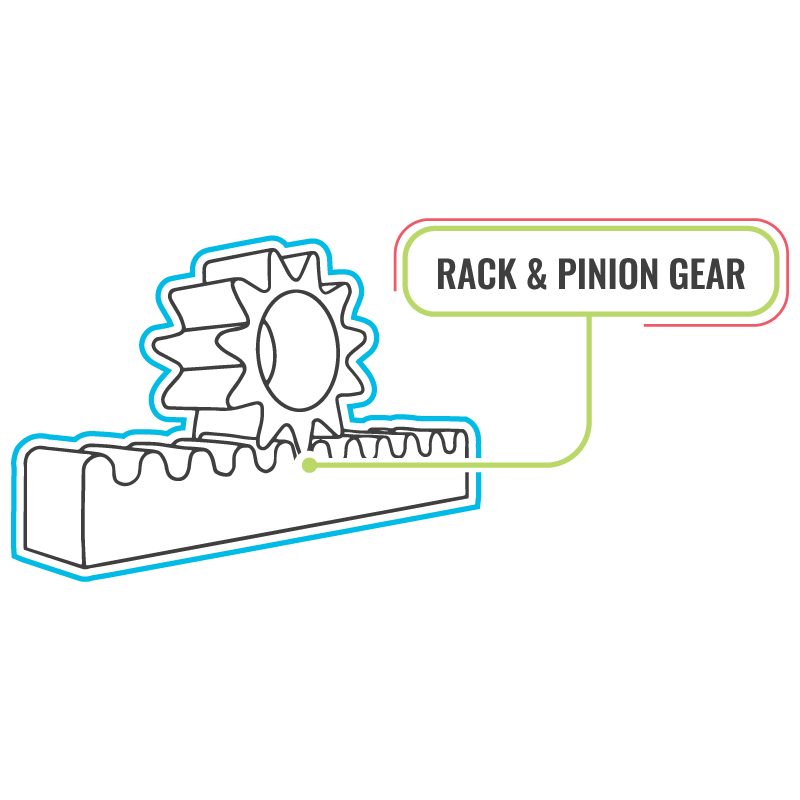
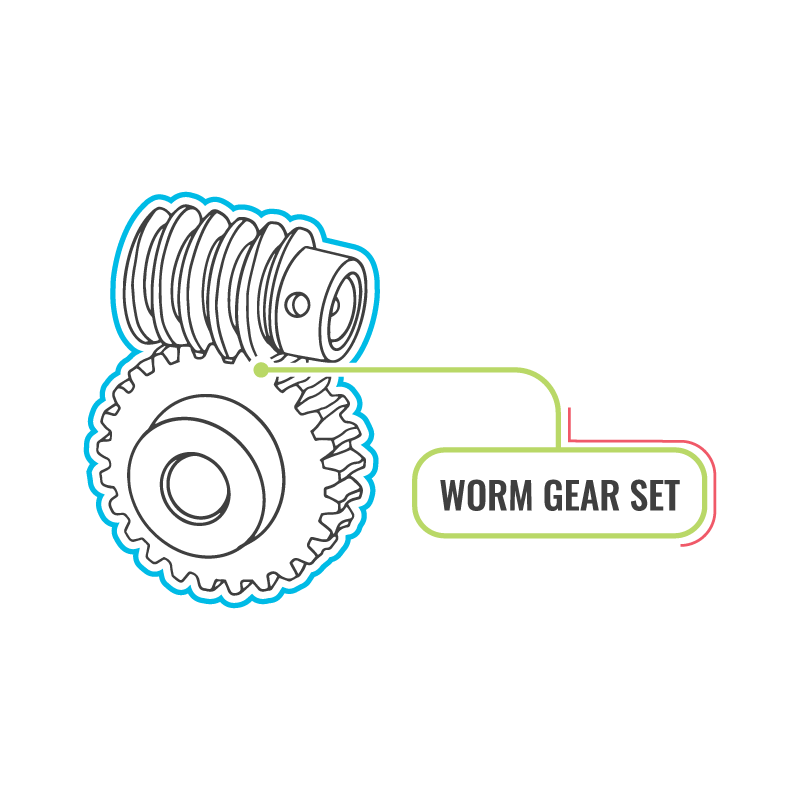
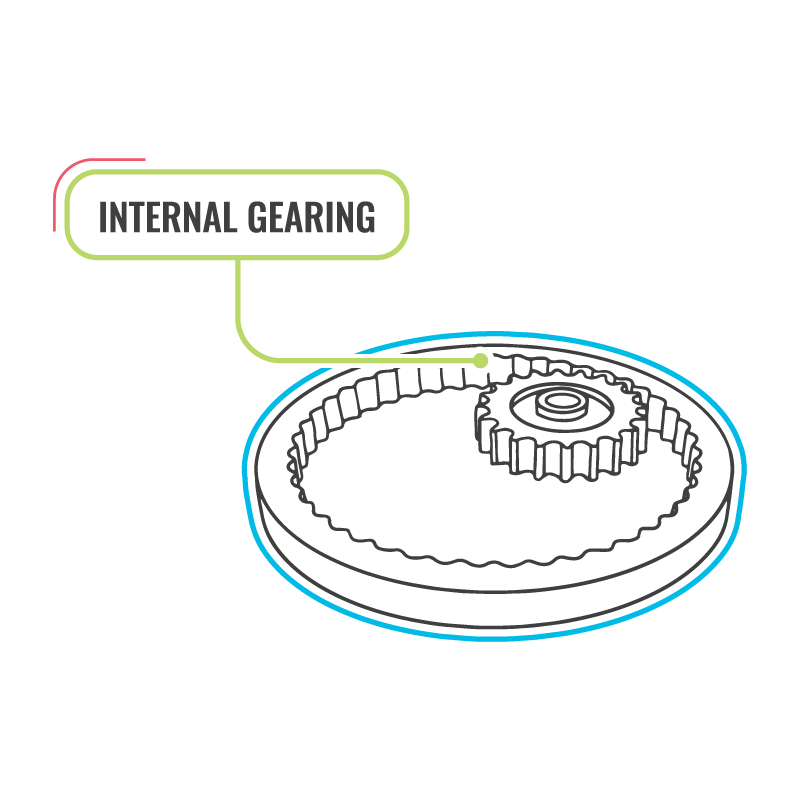
Gear Hobbing
Hobbing is a generative machining process for cutting external teeth. The cutting tool, called a hob, and part blank are in a synchronous rotation allowing all the teeth to be progressively cut in the part as the cutting tool moves axially across the part. A wide variety of teeth forms can be produced on a hobbing machine, such as:
Our hobbing department offers a wide variety of capabilities, including carbide rehobbing, high-helix hobbing, worm milling, and automation. With more than 15 pieces of equipment, we have plenty of capacity for any gearing needs, including spline lengths up to 500mm and diameters up to 400mm.
Carbide Rehobbing / Skiving:
The carbide rehobbing process utilizes a carbide hob to remove equal amounts of material from a rough-cut heat-treated gear. Carbide rehobbing eliminates distortion caused by heat treating, allowing us to achieve gear quality of AGMA 9 or better and is very economical compared to gear grinding.
Crown Hobbing:
This process produces a barrel shape on the flank of the gear tooth that compensates for misalignment and reduces noise. This application is especially advantageous with high-speed spur and helical pinions.
Our gear hobbing machinery:
Shaping
Shaping is a generative machining process for cutting external or internal teeth using a special cutting tool, called a shaper cutter, moving in a reciprocating cutting motion. The shaping cutting motion is ideal for gear manufacturing in tight spaces with limit clearances between teeth and adjacent surfaces.
Our shaping department is among the most modern and productive in the world. Each of our 7 gear shapers are equipped with electronic guides that allow us to produce helical teeth and lead crowning. With these machines, we can cut face widths up to 200mm, diameters up to 500mm, compensate for tapers, and machine at speeds up to 1500 stroke per minute.
Shaping can form a lot of the same features as hobbing, but with greater precision on both the inside and outside of a part.
Our shaping machinery:
Grinding
Gear grinding removes surface material through abrasion or micro-machining, using a grinding wheel rather than a cutting tool, ensuring the creation of proper tooth geometries. Gears with precision-ground teeth generally run more quietly than gears that have only been hobbed or shaped due to their higher precision and better surface finishes.
Grinding is used to create a number of features on parts:
FCG has two styles of gear grinders:
Form Grinders:
produce one tooth gap at a time, allowing extreme control and nearly unlimited tooth form modifications.
Our form grinding machinery:
Generating Grinders:
produce all teeth continuously, like hobbing, and allow for extremely fast production and quality.
Our generating grinding machinery:
Hob & Shaper Cutter Sharpening
We can sharpen both hobs and shaper cutters in-house with our Koepfer KFS-100 hob sharpener and Star PTG1 tool grinder. This allows us to recondition cutting tools during long production runs, which limits downtime, need for additional cutters, and increases efficiency.
Broaching
Broaching is the process of moving a stepped cutting tool, called a broach, through the bore of a part to create an internal spline or keyway. FCG’s broaching machine has 5-ton pulling capacity and 48” stroke.
Deburring
Deburring is the process of removing raised, rough metal on the edges and tips of gear teeth. FCG’s gear finishing department is extremely meticulous about our customers’ parts being completely free of burrs, foreign objects, or debris, and visually inspects every single part prior to shipping orders with digital optics such as bore scopes and microscopes.
Turning
Turning is a machining process using a stationary cutting tool and a rotating part to remove material to form the customer’s “blank.” At FCG, we utilize the most precise lathes to create the highest quality gear blanks. These machines hold the tightest external and internal features that support future grinding and gear cutting operations. Many of our lathes are equipped with y-axis and live tooling that allow for cross-axis machining to be completed in the same operation.
Our turning machinery:
Milling
Milling is a machining process using a rotating cutting tool and a stationary part to remove material to form features on a gear blank. At FCG, we utilize the most accurate 3- and 4-axis mills to machine proper features such as complex profiles, hole patterns, slots, keyways, and much more. In the future, FCG hopes to even add a true 5-axis machining center to complete our customers’ most challenging needs.
Our milling machinery:
OD/ID Grinding
This is a cylindrical grinding process that occurs on an external or internal surface of a part while the part is being rotated.
- OD (outer diameter) grinding of bearing journals, sealing surfaces, gear ODs, and tooling
- ID (inside diameter) grinding of bores and tapers in gear blanks and tooling
Typically, OD/ID ground parts have tight tolerances concerning size, runout, surface finish, and true position. These parts are also usually hard and are mostly finished, so extremely delicate handling is needed.
Our OD/ID grinding machinery:
Bore Honing
This is a process of finish machining the bore of a part to a precise size, position, and surface finish. An abrasive mandrel and oil are used to finish these typically hard bores.
Lapping
Lapping is a machining process in which two flat disc elements are rotated against opposite part faces with an abrasive slurry. This process is used to create surfaces with precise requirements for flatness, parallelism, size, and surface finish.
Laser Marking
This process refers to the technique of marking or labeling a gear using a laser machine, much like engraving. Many gears are laser-marked with serial numbers for traceability due to the critical nature in which the gear may operate. We also mark our tooling for easy identification, which will improve the quality of parts and efficiency.
Superfinishing
Also known as micro-machining, micro-finishing, REM superfinishing, fine grinding, and hard finishing. In this metalworking process, the part is placed into a vibratory bowl with pieces of ceramic and a chemical additive. The chemical reaction that occurs removes peaks from the machined surface, and leaves the part with a smooth microfinish that virtually eliminates the peaks and valleys present. Superfinishing a part will decrease friction and increase durability, efficiency, and performance. This is a process that improves surface finish for reduced friction and increased efficiency during operation.